How to solve 5 costly, risky, and time-consuming clean-up challenges in the Mining Industry
In any high-volume mining or bulk material handling operation, keeping conveyor systems and processing areas clean and functional is essential — yet achieving this can often require full production shutdowns, intensive manual labour, or costly third-party intervention.
The Dugless 903® remote-controlled mini loader offers an innovative and cost-effective solution to these long-standing problems.
Designed to eliminate downtime, recover valuable spillage, and drastically improve workplace safety and productivity, the Dugless 903® doesn’t just fill a gap in the market — it fills the gap that other machines and manual processes can’t reach underneath conveyor systems.
Problem 1: Shutdowns for Clean-Ups
The Challenge:
In conventional settings, clearing debris under conveyor belts or within plant areas often requires a complete shutdown of machinery. This halts production and causes ripple effects across scheduling, output targets, and revenue. Even short downtimes can cost thousands of dollars per hour, especially when dealing with high-output operations like iron ore processing.
The Dugless 903® Solution:
The Dugless 903 enables clean-ups without shutdowns. Its ultra-low 560mm height and 50mm ground clearance allow it to access previously unreachable spaces — such as beneath conveyor belts — while the system remains operational. The result? Maintenance and clean-up tasks that would take days (and cost millions in halted production) now be completed in hours, with no production interruption whatsoever.
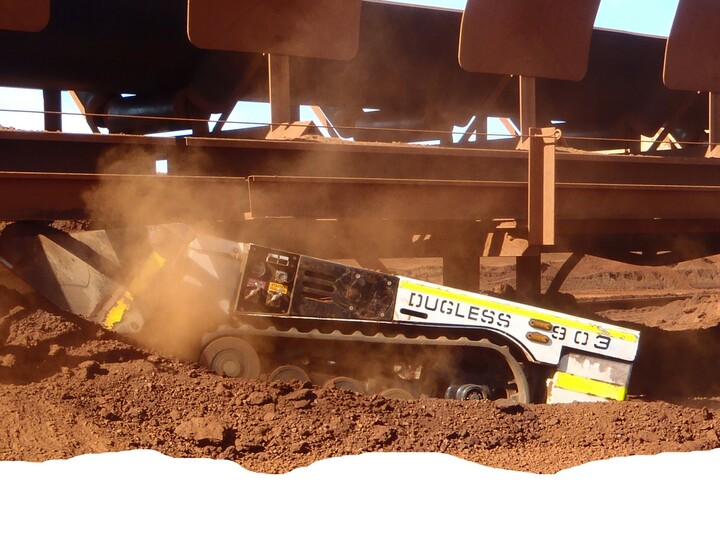
Problem 2: Unsafe Manual Labor Conditions
The Challenge:
Manual clean-up efforts in mining environments are not only time-consuming, but they also place workers in confined, dusty, and potentially dangerous spaces. Exposure to moving machinery, falling debris, and extreme weather conditions poses an unacceptable safety risk.
The Dugless 903® Solution:
Fully remote-controlled from up to 50 meters away, the Dugless 903 removes the need for personnel to enter hazardous zones. One operator, safely located outside the danger area, can manage the entire clean-up process using a simple two-joystick remote harness. This drastically reduces the risk of injury, lowers insurance liabilities, and meets stringent safety compliance standards.
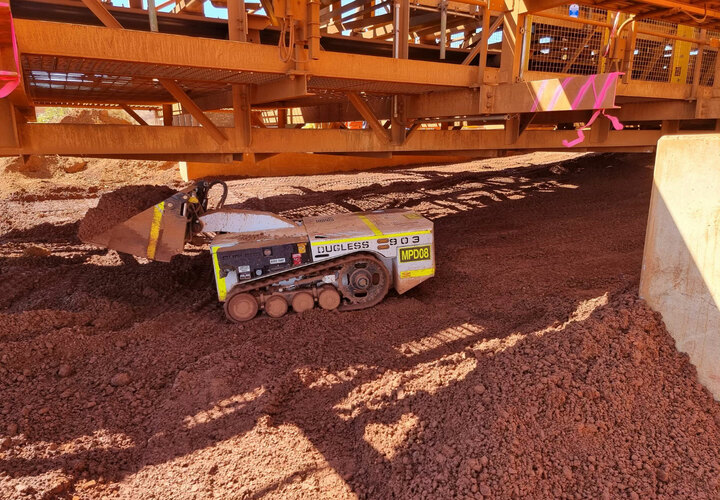
Problem 3: Limited Access for Traditional Machinery
The Challenge:
Traditional loaders and excavators are simply too large or cumbersome to access tight areas, especially beneath low-clearance conveyor systems or within narrow plant corridors. This limitation leaves significant quantities of valuable material unrecovered and operational zones prone to equipment damage.
The Dugless 903® Solution:
At just 1050mm wide and 2255mm long, the Dugless 903 is compact and highly manoeuvrable. Its tight turning radius and 4-in-1 self- leveling bucket (0.13m³ capacity) allow it to work effectively in the most constricted spaces. With front and rear rotation and only 960kg of weight, it can operate on various surfaces without causing structural stress or floor damage.
Problem 4: Material Loss and Wasted Resources
The Challenge:
Ore spillage and debris under belts isn’t just mess — its lost product and money. Over time, this build-up not only represents a waste of resources but can also interfere with machinery, reducing the operational lifespan of equipment like return rollers and belts, which can cost millions to replace.
The Dugless 903® Solution:
By efficiently collecting and relocating built-up ore, the Dugless 903 turns waste into profit. In one real-world case, a single unit reclaimed 50 tonnes of iron ore in just 3 days — material that was reintroduced into the operation. In another, 100 tonnes of iron ore were recovered under 200 meters of conveyor belt without requiring a single hour of downtime. That’s pure yield, previously written off as inaccessible waste.
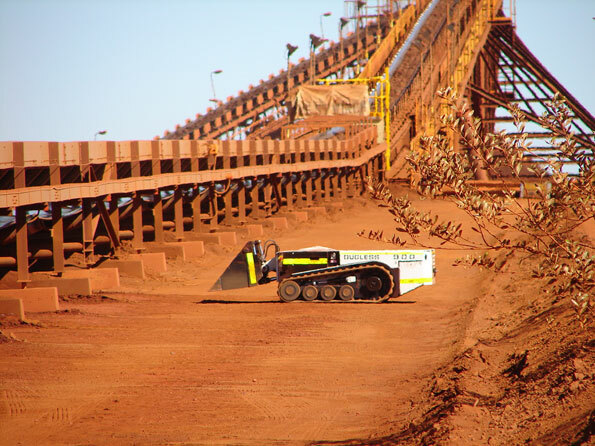
Problem 5: Equipment Downtime Due to Roller Damage
The Challenge:
Ore buildup under conveyors doesn’t just take up space — it causes return rollers to seize, belts to misalign, and expensive wear to set in. Left unaddressed, this leads to premature failure and multi- million-dollar repair or replacement bills.
The Dugless 903® Solution:
By consistently clearing debris from beneath critical areas, the Dugless 903 extends the life of conveyor components and prevents unscheduled maintenance emergencies. In fact, one site that deployed the Dugless prevented imminent roller failure entirely by removing dense spillage before it caused mechanical damage.
Key Features That Deliver These Benefits
• No shutdown required: Operations continue while the Dugless does its job.
• Safe operation: Remote control keeps workers out of harm’s way.
• Ultra-compact design: Reaches where other machines (and people) can’t.
• Self-leveling 4-in-1 bucket: Versatile for debris of various types and densities.
• Efficient spillage recovery: Turns lost material into usable product.
• Increased plant life: Reduces wear on belts, rollers, and drive systems.
• Low maintenance and easy to use: Operated by one person using a simple two-joystick interface.
• Upgraded 8-chamber cyclonic airbox: Protects internal components and ensures long-term reliability in dusty environments.
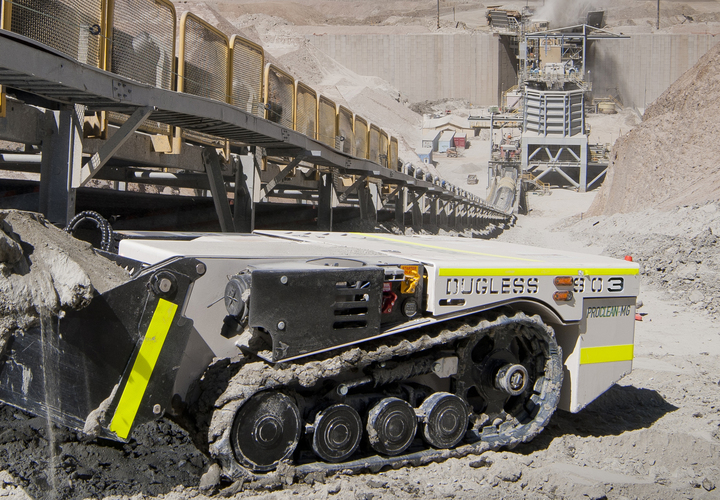
In Summary: What the Dugless 903 Solves
Problem Dugless 903® Solution:
Costly shutdowns Clean while running — no downtime
Manual labour risk Remote operation = no workers in danger zones
Inaccessible spillage Compact design fits under low-clearance belts
Lost product Recovers and reinstates valuable materials
Equipment wear/failure Prevents debris build-up and component damage
Low ROI on clean-ups High-value recovery, low operational cost
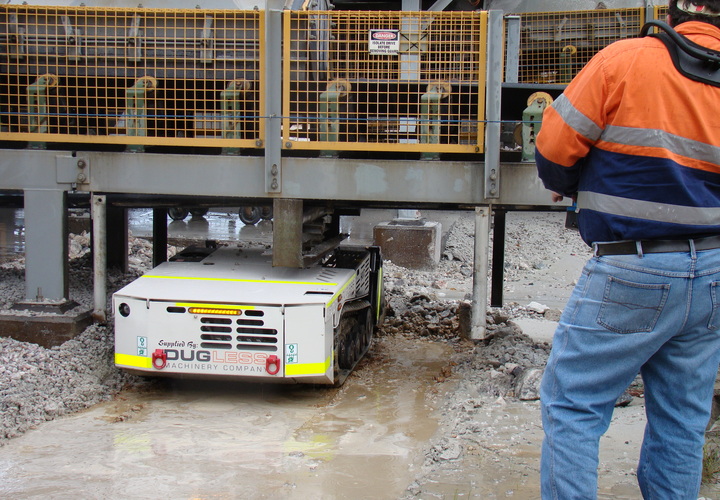
Make the smart decision and let the Dugless 903® work for you!
Custom built with precision and tailored to meet site specs, solve many costly, risky, and time-consuming clean-up challenges in the Mining Industry with this one solution. Secure the 903® this financial year. Stock moves fast, unlike the long-ignored spill zones, email us today and transform how your site handles cleanups.
Dugless 903® – the solution you’ve been waiting for.